A rivet is a permanent mechanical fastener that is designed to join two or more parts together, and there are numerous types of rivets. Each rivet is composed of a head, a shank, and a tail. To install, a rivet is inserted into a slightly oversized hole, then undergoes a process that permanently deforms it via a compressive force. This permanent deformation is achieved using a range of tools that are dependent upon the type of rivet being used.
In general, rivets are installed via pneumatic or manual hammering, hydraulic pressing, and handheld rivet guns that are either manually or pneumatically operated. When selecting rivet sizes, it’s critical to consider the grip length and the size of the hole. Many different grip lengths are available for each hole size to accommodate different sheet thicknesses. Rivets are typically made from either aluminum or steel, though other materials like copper are also used. Industries that most commonly rely on the use and function of rivets include the automotive, aerospace, marine/naval, construction, aviation, and manufacturing industries.
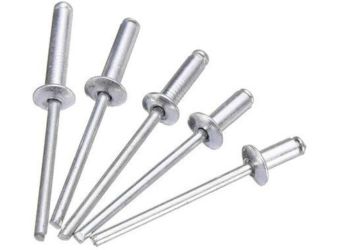
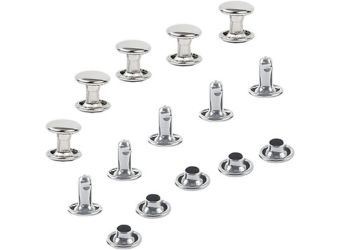
Materials Used for Rivets
Rivets are made from a range of different materials suited to specific applications. These materials are listed below:
- Aluminum: Aluminum rivets are the most common. They’re lightweight and have good corrosion and weathering resistance. These rivets can be easily deformed and, as such, blind rivets made from aluminum can be installed with a hand-operated rivet tool.
- Stainless Steel: Stainless steel rivets have excellent corrosion and weathering resistance. However, due to their hardness, they’re difficult to install with hand-operated rivet tools. Pneumatic rivet guns are recommended for installing blind stainless steel rivets.
- Copper: Copper has excellent electrical and thermal conductivity in addition to being relatively easy to form.
- Steel: Carbon steel rivets are usually solid or hollow shank and must be installed using pneumatic or hydraulic equipment. Low-carbon steel is preferred as it is more ductile than rigid, high-carbon steel.
- Brass: Brass is an alloy of zinc and copper that has exceptional corrosion resistance and strength, and cannot spark. These properties make brass rivets ideal for applications in the oil and gas industry. They are also used for their aesthetic appeal.
It must be noted that some materials can be prone to creating a galvanic corrosion cell. As such, rivet materials must be chosen carefully to ensure compatibility with the material being fastened.